Most industries have some kind of performance indicators on their equipment such as up time, units produced, and sometimes even the production speed. These are appropriate things to look at if the focus is on what’s coming out of the machine.
Total Productive Maintenance (TPM) takes a slightly different approach. Besides what’s coming out of the machine, we also want to know what could have produced, and where we are losing effectiveness. Overall Equipment Effectiveness, or OEE, offers a simple but powerful measurement tool to get inside information on what is actually happening.
The OEE calculation is a metric that gives us daily information about how effectively the machine is running and which of the six big losses we need to improve. Overall equipment effectiveness is not the only indicator to assess a production system, but it is certainly very important if our goal is improvement.
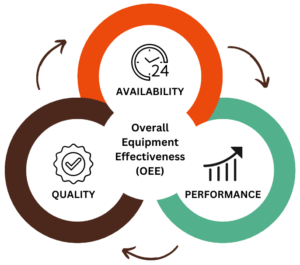
The Elements of Overall Equipment Effectiveness (OEE)
The three main categories of equipment-related losses —downtime, speed loss, and defect or quality loss— are also the main ingredients for determining the overall equipment effectiveness. Overall equipment effectiveness is calculated by combining three factors that reflect these losses: the availability rate, the performance rate, and the quality rate.
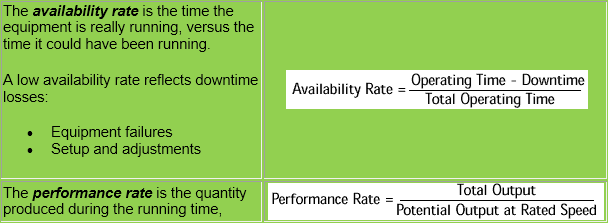
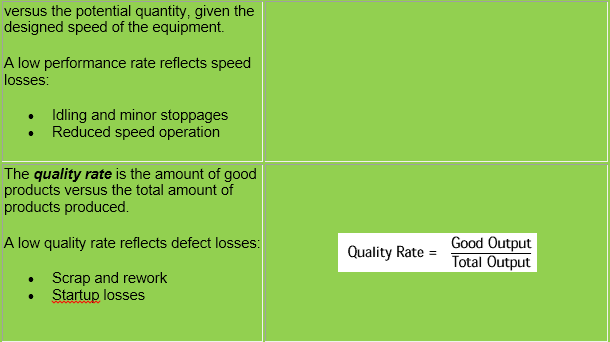
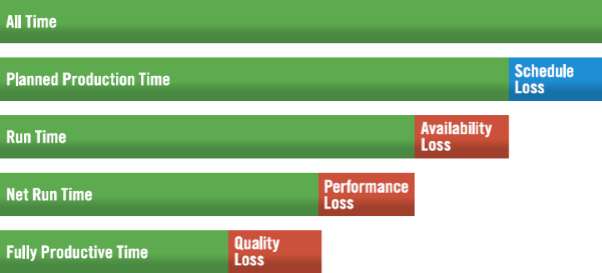
To calculate OEE, we multiply the three factors together:

Benefits of OEE Monitoring
The goal of measuring OEE is to improve the effectiveness of your equipment. Since equipment effectiveness affects shop floor employees more than any other group, it is appropriate for them to be involved in tracking OEE and in planning and implementing equipment improvements to reduce lost effectiveness. Let’s look at some of the benefits of OEE measurement for a manufacturing company.
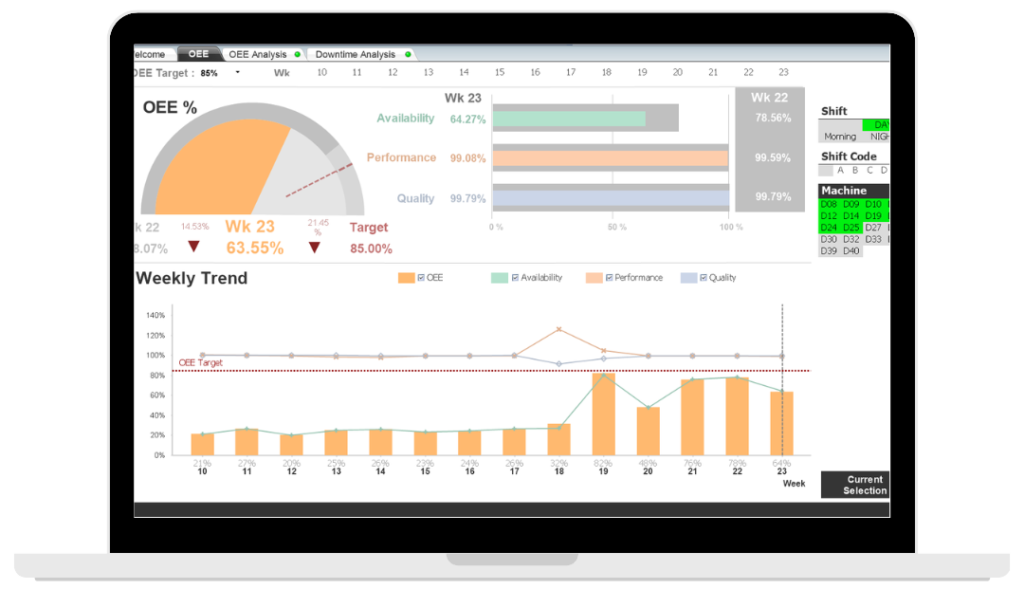
An OEE solution can enable manufacturers to achieve world-class status. More specifically, it can provide benefits in four key areas:
- Equipment: Reduced equipment downtime and maintenance costs, plus better management of the equipment life cycle.
- Personnel: Labour efficiencies and increase productivity by improving visibility into operations and empowering operators
- Process: Increased productivity by identifying bottlenecks
- Quality: Increased rate of quality, reduced scrap