Challenges of Statistical Process Control (SPC) Implementation in Malaysia Manufacturing Companies Introduction
For the past ten years, Malaysian manufacturing companies facing tough competition especially due to rising customer expectations on product quality, better services and lower production cost from the countries in this region such as Thailand, Indonesia ,Vietnam, etc.
In order to compete and survive in global competitive market place, Malaysian manufacturing companies are trying hard to improve their product quality, cost competitiveness, efficiency, productivity and technology.
In view of quality expectation from customers is getting higher, manufacturers can’t rely on traditional quality management approach which is very much focus on corrective action or “fire fighting”. Engineers need to be more proactive to prevent defects or rejects being produced.
In recent year, the use of Statistical Process Control (SPC) and statistical method is emphasized. Nowadays, it becomes a mandatory requirement for most of the contract manufacturers. The use of SPC and statistical methods for variation reduction are core philosophies of Continuous Improvement and Total Quality Management.
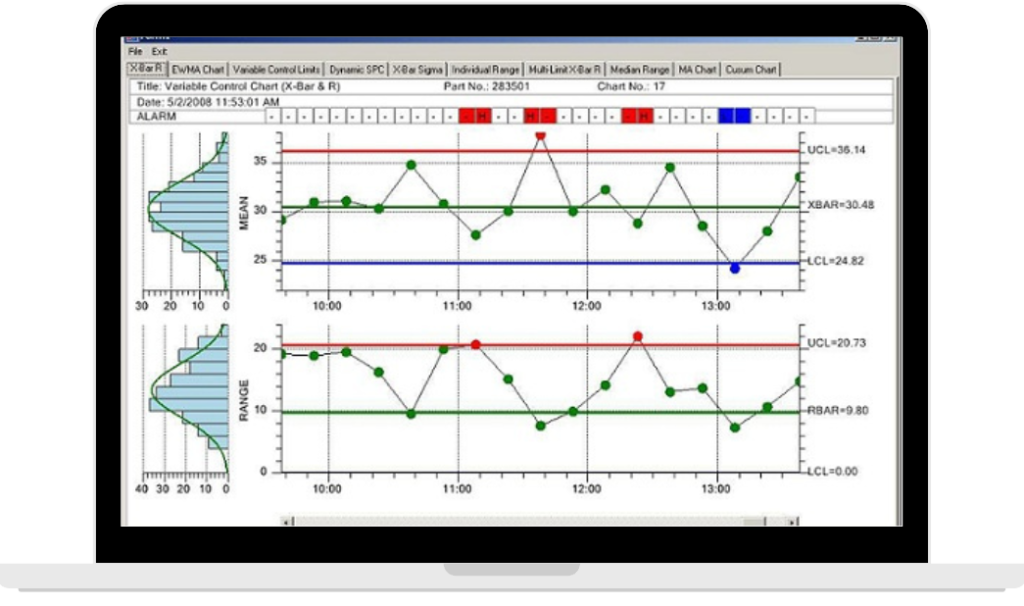
Traditional quality control suffers in that it is reactive to problems with an overemphasis on inspection and sorting. Continuous improvement philosophies are proactive with a focus on prevention and early detection of problems. Continuous improvement philosophies are data – driven with the use of defendable statistical methods for diagnosing problems.
SPC, Design of Experiments, and the use of statistical methods to quantify variation are key principles of the more contemporary Six Sigma Quality and Lean Six Sigma (LSS) philosophies. Six Sigma Quality and LSS philosophies promote reduction in long term variation so that only 3.4 parts per million defective are manufactured. What business person would disagree with such philosophies?
Challenges
Although the role of SPC is critical to achieve better product quality, however the implementation of SPC in most of the Malaysian manufacturing companies is not satisfactory. Traditional way of implementing SPC is no longer suitable in today highly competitive market place.
Typically, when a manufacturer implements a quality control procedure that involves measuring something, they start by purchasing a measuring instrument (e.g. a caliper, micrometer, height gage, bore gage, force gage, CMM, etc.) from one of the many metrology companies. The manufacturer might then develop a procedure for measuring their parts where someone is given the task of taking measurements and writing them down on a piece of paper. The measurements would then be keyed into either a spreadsheet or a dedicated SPC software program for analysis by an engineer. Obviously this method has a lot potential pitfalls since people are involved in the manual data collection and data entry part of the process. Manual data entry is slow and tedious and people make mistakes.
Possible Solutions
A more accurate and more efficient approach to data collection is to enter data from your measuring instruments directly into a spreadsheet or SPC program. Most measuring tools today are available with some form of electronic output making it possible to connect the instrument to data loggers, printers or to a computer, thereby eliminating the steps of manually writing down measurements and typing them in.
Automating data collection removes all possibility of human error and it also allows for real time data analysis. In addition to collecting an accurate computerized record, it is also possible to control an entire process based on the input from the tools that you use to measure the process. From our previous example, when you measure each part that comes out of your cutting machine, the measurement can be fed immediately to a PC that has been programmed to instruct an operator to change the blade when the measurements fall outside a specific tolerance. This type of automation creates an extremely efficient process designed to maintain the manufacturers’ quality control standards.
Interestingly, the metrology industry has never settled on any one standard for the electronic interface between instruments. This is due, in part, to simple rivalries between companies. Each of the different “key players” in the measuring tool industry developed their own electronic interface with the hope of making theirs’ the standard for the entire industry. By protecting their interface standard with patents, they lock the competition out from any large manufacturer that adopts their electronic interface standard.